Quality Manual
Contents
Scope of manual
1.1
The purpose of this manual is to demonstrate and document the ability of Mid Valley Protofab, Inc. to provide a consistently high quality of work in accordance with the requirements and expectations of our customers.
1.2
The quality control practices and standard operating procedures described in the manual apply to all aspects of our work, specifically including: order processing, purchase order creation, distribution of drawings or technical information, preliminary inspection, ordering/issuing of materials, all aspects of the manufacturing process, final inspection, packaging, shipping, and billing.
1.3
Equipment calibration is fundamental to ensuring a high quality product. The methods of obtaining and maintaining calibrated equipment are documented herein.
1.4
Mid Valley Protofab, Inc. values a culture of continuous improvement. Any quality issues, whether internal or external, are indicative of an opportunity for improvement. The process for corrective actions described in this manual ensures that any issues are systematically evaluated and the relevant processes are reviewed.
QC Management Responsibility
2.1
The Vice President of Operations reports to the President and serves as the manager responsible for oversight and direction in regards to quality control.
2.2
The Vice President of Operations responsibilities in terms of managing quality consist of the following:
a. Communication of all expectations related to quality control.
b. Investigate any quality exceptions to determine the root cause.
c. Identify and implement corrective actions necessary to resolve a quality exception.
d. Responds to any customer inquiries regarding our quality control methods and procedures.
e. Coordinates any customer-initiated audits of our quality systems.
f. Oversees maintenance of calibration records for measuring equipment.
g. Generation of customer specific incoming/outgoing inspection reports as needed.
h. Ensure work order instructions are consistent with customer expectations.
i. Ensure all appropriate drawings and technical information are clearly conveyed to shop personnel.
j. Ensure appropriate materials are specified and used in adherence with customer requirements.
2.3
The President bears the responsibility for training on this manual and conducting internal audits for compliance, or his/her designee.
2.4
All managers and employees are required to comply with all provisions of this Quality Manual as it relates to their specific operational responsibilities.
Order Processing
3.1
All jobs, both quoted and time and material, require customer to furnish a purchase order or written authorization from a qualified customer representative before work can begin. “Written authorization” includes an email.
3.2
Any purchase orders received via email is to be forwarded to Administrative Support for processing.
3.3
All customer purchase orders or written authorizations are saved to our NAS Data Station for archival purposes.
3.4
Upon release of purchase order the customer is to provide MVP with any necessary documents required to complete the work such as drawings, customer specifications or requirements.
3.5
A Job Traveler is generated by Administrative Support, using ISS Software or a Manual Traveler from which the purchase order information is taken. The Job Traveler is to be reviewed for accuracy versus the purchase order by shop personnel and shop supervisors. The customer will be notified in the event of any discrepancies.
3.6
The job Traveler is then distributed to programming or to the shop floor along with any other supplementary documents (such as drawings or inspection sheets) and serves as the governing document regarding the job.
3.7
Changes to the scope of work of a job must be confirmed by the customer with written authorization from a qualified customer representative.
3.8
Any changes to the scope of work of a job require an updated & revised drawing from the customer. The changes are then documented via a revision to the Job Traveler or Manual Traveler. All existing Travelers and drawings are to be pulled from production and replaced with the revised documents. The revision is confirmed to the customer via an email.
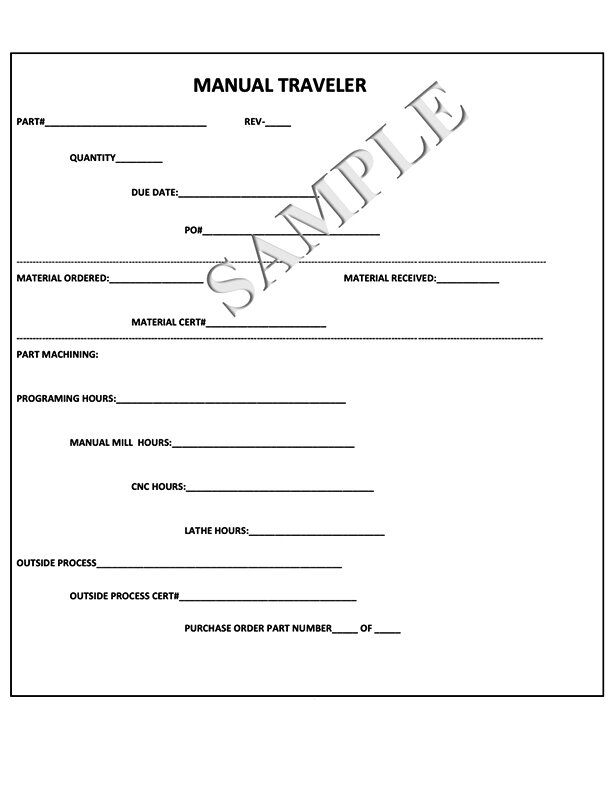
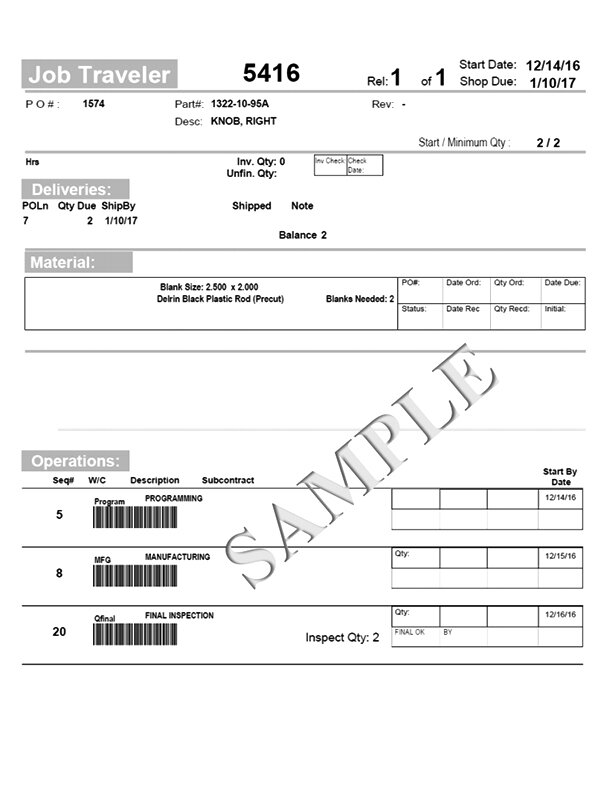
Engineering Drawings
4.1
All engineering drawings are kept in our drawing files. These drawing files are managed and maintained by Administrative Support and Programming.
4.2
A PDF File of the drawing used on each job is kept in the relevant job folder, for purposes of reference and history.
4.3
Any CAD drawing or sketch produced by Mid Valley Protofab, Inc. is assigned a drawing number or name and is stored in the relevant job folder.
4.4
Copies of drawings are distributed to the floor by Programming and are collected at the completion of each job.
4.5
In the event that drawings for a job are unavailable, work should be performed in accordance with the specifications documented on the Job Traveler, from working sketches, and per customer instructions.
Incoming Inspection
5.1
All customer equipment received with intent to repair is to be cleaned and inspected as needed to properly evaluate the condition of the part or system.
5.2
Customer-supplied incoming inspection sheets and processes will be completed as requested, provided the request is made prior to quoting the job. In the event that no inspection sheet is supplied by the customer, no report will be generated.
Inventory Control
6.1
The Vice President of Operations is responsible for verifying all incoming stock materials for correct dimensional accuracy, and verify that they match PO descriptions.
6.2
Once verified, all materials are to be received into inventory and stored in their designated locations.
6.3
The types and quantities of materials to be stocked are determined by the purchasing department.
6.4
All incoming materials ordered for specific jobs are to be identified with a certification number and/or a job number and are to be placed in the staging area, away from standard stock.
6.5
Raw material certifications will be provided to the customer only on an as requested basis. Requests for certifications must be made prior to quoting the job.
6.6
All materials must be ordered via a Material Order form or an online order both requiring a purchase order in ISS placed through Purchasing.
6.7
Materials used on a job are to be designated as such on the PO and on the Job Traveler.
6.8
Material inventory is audited at least annually for correctness of type and quantity versus system records.
Final Inspection
7.1
All work is to be performed in accordance with customer specifications.
7.2
In the event that no customer drawing is available, work is to be performed in accordance with the specifications documented on the purchase order, from working sketches, per customer instructions.
7.3
Upon completion, all work must be inspected by the employee performing the work. Each part is then placed on the inspection rack for inspection by the Inspection Department, which will use the means of either manual or CMM inspection instruments. The MVP Compliance Inspection Form or a CMM generated Inspection Report will be used to document all relative measurements only when requested by the customer, which must be requested before the job is quoted.
7.4
For part modification work, the scope of the final inspection is to include only dimensions affected by the work performed by MVP.
7.5
For new parts made, the scope of the final inspection is to include all machined features and drawing dimensions. For orders of multiple parts a sample of 10% of parts will be inspected, unless otherwise requested by the customer.
7.6
In the event parts contain features which cannot be measured with conventional measuring tools, shop management will develop a plan for inspection.
7.7
Customized inspection programs for equipment or projects will be developed as requested by the customer. Such requests must be made prior to quoting the job.
7.8
In-process inspection will be performed after each manufacturing process by the employee machining the part. Job specific expectations for any in-process inspection will be supplied by the Inspection Dept.
7.9
Each job that requires an outsourced process (i.e. welding, bending, laser, etc.) will have an in-process inspection by the Inspection Dept. upon arrival.
7.10
At the completion of each job the assigned supervisor is to review the work to verify that it has been carried out as instructed on the Job Traveler, and that all work was performed with good workmanship.
Identification, Packaging and
Shipping
8.1
All work is to be clearly marked with the customer name and a job number immediately on arrival.
8.2
A Job Traveler is to be generated in a timely manner, once the scope of work is determined.
8.3
The Job Traveler is to be attached to the job drawings and forwarded to the Programming Dept. for shop distribution. It is to stay with the work throughout the manufacturing process.
8.4
On completion, all work is to be packaged in accordance with purchase order instructions. In the event that no specific packaging instructions are specified on the PO, MVP will package the parts using industry standard methods such as by pallet.
8.5
Work received in a customer-supplied container will be returned in the same container.
8.6
On quoted jobs the shipping method is defined on the quote. Additional shipping charges may apply for jobs outside of our standard delivery region or for jobs that require transport on a semitrailer.
8.7
When a job is delivered to a customer, they are given a copy of a packing slip documenting the parts shipped to them. A signed copy of the packing slip is kept in the job files at MVP to document the delivery of the job to the customer.
Billing
9.1
Our job is not finished until the invoice is sent, and our goal is that all invoices will be sent promptly and accurately to the appropriate contact.
9.2
Each bill is expected to have a clear description of the services rendered and accurate pricing for these services.
9.3
On Time and Material jobs, a price update is available at any time upon customer request.
9.4
Appropriate customer documents, such as purchase order number, requisition number, or equipment serial number shall be referenced on the final invoice.
Equipment Calibration
10.1
An Inspection Room is maintained for the control of all inspection equipment and gages. A system is in place to control the issue and return of all equipment released from this area.
10.2
All standards are certified annually. Certification documents are kept on file in the Inspection Room and are available for customer review upon request.
10.3
All micrometers, both personally and company owned, are set to standards once annually. These records are maintained and stored in the Inspection Room.
10.4
The Inspection Room manager ensures that micrometers are properly set to a standard each time a micrometer is checked out of the Inspection Room.
10.5
Annual training is done to ensure that all necessary personnel know how to properly set micrometers to standards.
10.6
Quality checks such as vibration analysis and leveling are performed as part of a preventative maintenance program at least annually on each machine, or as symptoms are observed. Any problems found are recorded in the Maintenance files.
10.7
Reference the Instrument Calibration Record to see a full list of all calibrated equipment.
General Workmanship Standards
11.1
Unless otherwise indicated on engineering drawings, all Shop work is to conform to the general workmanship standards.
11.2
Machining:
a. All machined surfaces are to be free of nicks, scratches, and are to have a 125 micro-inch Ra finish or better.
b. All sharp edges to be broken and de-burred.
11.3
Welding:
a. All welds are to be free of slag, inclusions, and porosity.
b. Weld beads are to be uniform and consistent.
c. Welded equipment is to be preheated and post-heated in accordance with sound welding practices for the given materials. If base material is not known, it will be welded with the caution necessary for welding high carbon steels.
11.4
Grinding:
a. All ground surfaces are to have a 32 Ra finish or better, unless otherwise specified.
b. All ground surfaces are to be free of traverse lines and chatter marks. c. All sharp edges to be broken and deburred.
11.5
Thermal Spray:
a. All thermal spray coatings are to be uniform and consistent.
b. Coating roughness should be in accordance with material and process specifications.
c. Coatings should be free of coarse grains indicative of improper application.
11.6
Disassembly/Reassembly:
a. All components to be dimensionally checked for proper fit prior to assembly.
b. When installing bearings and seals, all manufacturer-recommended standard practices are to be observed. This includes recommended bearing fit.
c. Service-removable thread locking compound is to be used on all fasteners as a standard practice. Other types of thread locking compounds may be used depending on customer requests and the application.
Corrective Action Procedures
12.1
All possible precautions are taken to ensure that quality exceptions never occur. In the event that an exception does occur, the highest priority is given on getting an acceptable part to the customer as soon as possible.
12.2
As part of our continuous improvement philosophy, any quality exception is viewed as a potential to improve.
12.3
For any quality exception, whether discovered internally or by a customer, a rework analysis is performed. The purpose of this analysis is to understand the root cause of the issue and to identify measures that can be taken to prevent similar issues from occurring in the future.
Internal Audit System
13.1
An internal audit system is in place to verify that all policies and practices outlined in this manual are being carried out.
13.2
The President, Vice President and assigned managers bear the responsibility for conducting and reviewing internal audits.
13.3
Full audits are to be conducted at least annually. Partial audits may be conducted if concerns of adherence to specific areas of the program arise.
13.4
Once complete, audits are reviewed by management. Any concerns identified during the audit will be addressed by the supervisor of the responsible department.
13.5
All completed audit paperwork will be kept on file in the office of the Vice President.
Training
14.1
All employees are to be trained on the contents of this manual when hired. 14.2 Each employee is to be given a copy of this manual for reference.
14.3
Follow-up training may be carried out in the event of revisions to the manual.
14.4
The training program is conducted by the President, Vice President and assigned managers.
Revisions
15.1
All revisions to this manual are to be documented in the form below.
15.2
The revision number of the document is to be displayed in the footer of each page and is to be updated with each revision.